El mapa de flujo de valor consiste en el modelado de un estado real mejorado por medio de una reducción específica de la duración del proceso.
En la práctica, el mapeo de valor se ha convertido en una actividad esencial ante la formulación de planes de mejora, de tal manera que forma parte del diagnóstico del proceso (VSM actual) y de la proposición de estrategias de mejoramiento (VSM futuro).
Al realizar un mapa del flujo de valor debemos responder una serie de cuestiones críticas relacionadas con las operaciones:
- ¿Cuál es la capacidad del sistema de producción?
- ¿Cuáles son los cuellos de botella del proceso?
- ¿Cuál es la tasa de compra del cliente?
- ¿Cuál es la capacidad disponible, y cuál su utilización?
- ¿Cuáles son las restricciones del proceso? ¿Estas son internas o externas?
- ¿Cómo podemos mejorar el proceso para cumplir con los objetivos del negocio?
Indicadores relevantes de un Mapa de Valor
Tiempo TAKT
El tiempo takt es un indicador de la frecuencia de compra del cliente. Para muchos expertos se trata de un tiempo objetivo al cual el sistema de producción debe adaptarse para satisfacer las expectativas del cliente. Se calcula de la siguiente manera:
Tiempo takt = Tiempo disponible / Demanda
Por ejemplo:
Jornada laboral: 8 horas por turno
Tiempo de almuerzo: 0,5 horas por turno
Número de turnos: 1 turno diario
Días hábiles por mes: 22 días al mes
Demanda mensual: 7.510 piezas al mes
Tiempo disponible = (8 h/turno) – (0,5 h/turno) = 7,5 h/turno
Tiempo disponible = (7,5 h/turno) * (60 m/hora) = 450 m/turno
Tiempo disponible = (450 m/turno) * (1 turno/día) * (60 s/min) = 27.000 s/día
Demanda diaria = (7.510 piezas/mes) / (22 días/mes) = 341 piezas/día
Tiempo Takt = (27.000 s/día) / (341 piezas/día) = 79 s/pieza
Es decir, que un cliente compra una pieza cada 79 segundos, de tal manera que el tiempo estándar por pieza debe ser igual o inferior a 79 segundos.
Tiempo de ciclo individual
Es el tiempo estándar asociado a cada operación del proceso. Por ejemplo: El tiempo asociado a pintar una pieza, o el tiempo estándar asociado a empacarla.
Tiempo de ciclo total (Lead Time de fabricación)
Es el tiempo que duran todas las operaciones, se calcula sumando los tiempos de ciclo individuales.
Tiempo de previsión de las necesidades del cliente (Lead time GAP)
En este intervalo de tiempo es cuando se deben realizar las previsiones respecto a los puntos y cantidades de pedido futuras. La magnitud del GAP es directamente proporcional con los errores en las previsiones.
Tiempo de entrega logística (Lead Time Logistic)
Comprende el intervalo de tiempo que tarda la organización desde que se abastece de materias primas, materiales e insumos hasta que el producto terminado es distribuido al cliente.
¿Cómo realizar un Mapa de Valor paso a paso?
Simbología básica de un Mapa de Valor (VSM)
Fuentes externas: Este símbolo representa clientes y proveedores.
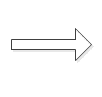
Transporte mediante camión de carga.
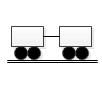
Transporte mediante tren.
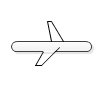
Transporte mediante avión.
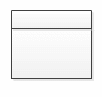
Proceso.
Información: Pronóstico, plan de producción, programación.
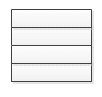
Casillero de datos con indicadores del proceso.
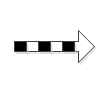
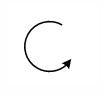
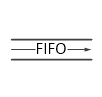
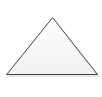
Inventario: De materia prima, producto en proceso, producto terminado. Debe indicarse tanto la cantidad como la duración estimada.
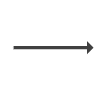
Información transmitida de forma manual.
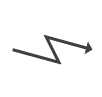
Información transmitida de forma electrónica.
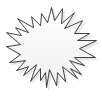
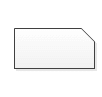
Kanban de producción.
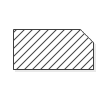
Kanban de transporte.
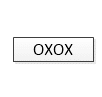
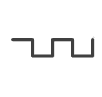
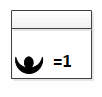
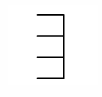
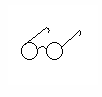
Establecer familias de productos
Para poder identificar las familias de productos sobre las cuales aplicaremos el mapa de valor, es necesario tener en cuenta las operaciones por las que pasa cada producto, y el tiempo de ciclo individual de dichas operaciones.
Podemos afirmar que una familia de productos es un grupo de referencias que pasan por las mismas operaciones y cuyos tiempos de ciclo no varían mucho de una referencia a otra.
Registrar la siguiente información
- Tiempos de ciclo para cada operación del proceso.
- Disponibilidad de cada equipo del proceso.
- Tiempo de cambio de producto en cada operación (alistamiento).
- Inventarios en cada etapa del proceso.
- Conocer la demanda del cliente, los medios por los cuales solicita, la frecuencia y cantidad de los pedidos.
- Pronósticos utilizados para predecir la demanda y las necesidades de abastecimiento, los medios por los cuales se pide, la frecuencia y la cantidad de los pedidos que se hacen hacia los proveedores.
- Conocer la secuencia del proceso, el flujo de materiales y de información.
Pasos para construir un Mapa de Flujo de Valor
1. La construcción del mapa inicia colocando el símbolo del cliente en la esquina superior derecha del plano. Luego conectamos el flujo de información (manual o electrónica) por medio del cual se relaciona la demanda del cliente (pronóstico y pedidos reales) con el control de la producción. Acto seguido, se relaciona el control de la producción con los requerimientos enviados al proveedor con las previsiones del material, conectando el flujo de información por medio del cual se relaciona la necesidad de materiales con los proveedores.
2. El siguiente paso consiste en representar el transporte desde los proveedores hacia la empresa.
3. Dibujamos la secuencia de las operaciones estableciendo el tiempo de cada operación, el tiempo de cambio de producto, la disponibilidad de los equipos, el tiempo disponible y los inventarios en proceso.
4. Representamos el programa de producción que indica la cantidad que debe procesar cada operación, así como el flujo de información (manual o electrónica) que relaciona estas operaciones. Además representamos el transporte desde la fábrica hacia los clientes.
5. Representamos mediante una escalera los tiempos de ciclo de cada operación (valor agregado) en la parte de abajo de los escalones; y el tiempo que no agrega valor en los escalones superiores. Los inventarios deben registrarse en función del tiempo y forman parte de lo que no agrega valor en el proceso. Para ello podemos dividir la cantidad de cada inventario entre la cantidad diaria requerida por el cliente.
6. Calculamos el tiempo takt:
Tiempo disponible = 27000 segundos / día
Demanda diaria = 500 unidades / día
Tiempo takt = 27000 / 500 = 54 segundos / unidad
Esto significa que el cliente compra con una frecuencia promedio de 54 segundos por día, de tal manera que este tiempo debe ser nuestro objetivo de producción. Ya en el Mapa de Valor podemos observar que existen procesos por mejorar e inventarios por reducir. El paso siguiente será entonces, construir el Mapa de Valor futuro en el cual deberán identificarse los eventos Kaizen de mejora.
NO ENTIENDO COMO ES QUE EL INVENTARIO VA CAMBIANDO CONFORME AVANZAN LAS OPERACIONES
en el casillero de datos, ¿que significa «el porcentaje de dispon???
Saludos, tendrás que me pudieras compartir el mapa de estado futuro con las mejoras establecidas para este ejemplo que detallas de mapa actual?????
No es lo mismo el tiempo de ciclo (TC) y el Lead time (LT), no siempre el lead time se corresponde con el tiempo de ciclo. En un horno en el que entran 4 pizzas por ejemplo, que necesitan de 10 mins de cocinado, el tiempo de ciclo es de 2,5 mins, pero el lead time es de 10 mins.
En el desarrollo del artículo se hace una definición de cada concepto: tiempo de ciclo individual y tiempo de ciclo total (lead time de fabricación).
Hola, yo tb tengo la duda del inventario, he visto algunos ejercicios de Vsm, en los cuales empiezan con un inventario de 120, luego pasan a 240, sigue con 180, no entiendo esa dinámica, y la otra no se si tengas un ejemplo aplicado a empresas de servicio, donde por ejemplo no tenemos un proveedor, sino que es sel cliente quien entrega de forma directa el insumo para que empiece el proceso, muchas gracias
Cómo calculo los inventarios entre proceso?
Es mi única duda, gracias!
La fluides de una linea de producción dependerá de elimiar los inventarios en procesos, ahora estos valores normalente los obtienes durante el proceso de fabricación que generalmente se reportan en las maquinarias que te presentan la restrincción por capacidad o cuello de botella