¿Qué implica Racionalizar?
Aunque estoy completamente seguro que la palabra racionalizar no te dice nada, al terminar este artículo verás que es bastante evidente cómo nos puede ayudar a aumentar la productividad.
Racionalizar implica mejorar el aprovechamiento de TODOS los recursos a los que tenemos acceso. Si recuerdas nuestro último artículo en el que hablábamos sobre aumentar los precios, introdujimos la siguiente gráfica en la que explicamos cómo ganamos dinero:
¿Cómo ganamos dinero?
Algo que seguramente notaron es que falta incluir un importante factor que a nadie le gusta: el costo.
Es importante incluir el costo para calcular nuestros beneficios.
Los consejos de hoy se centran en encontrar maneras de aprovechar los recursos que tenemos disponibles al máximo, para que los costos sean lo menor posibles. En la práctica y en un ambiente profesional, hemos visto que hay 3 caminos para lograr esto.
1. Mejorar el aprovechamiento de los Materiales
Si nuestro proceso implica transformar algún material para agregarle valor, seguramente vamos a generar algo de desperdicio en el camino. Este desperdicio tiene dos orígenes.
Desperdicio por el diseño del producto
Ya lo hemos platicado anteriormente: Los clientes compran valor. Y el valor está definido por los beneficios que nos aporta un producto sobre los sacrificios que tenemos que hacer para obtenerlos. Muchos de los costos innecesarios que tienen nuestros productos se deben a funciones que no le aportan beneficios a los clientes. O funciones redundantes que se repiten a lo largo de nuestro producto. Para ejemplificar esto (que es una ocurrencia en TODOS los productos) vamos a hablar de los Chindogus.
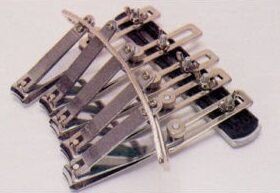
Los Chindogus son inventos que aparentemente son la solución ideal para un problema muy particular pero en la práctica resultan ser todo lo contrario. En la práctica son soluciones completamente absurdas a problemas cotidianos. Por ejemplo, aquí arriba encontramos que la función de cortar uñas está repetida 5 veces y esto aumenta los costos 4 veces (por fabricar 4 cortauñas adicionales) y un poquito más por fabricar y diseñar el mecanismo de soporte y unión de todo.
En tu producto, ¿Tienes soluciones que no le agregan valor a tus clientes?. O en caso de que no fabriques nada… ¿Tu proceso está diseñado para agregar más valor al cliente?
Las herramientas que te recomiendo usar para mejorar en este aspecto son Ingeniería de Valor en caso de que vayas a modificar físicamente un producto y Design Thinking para cambiar procesos que tienen que ver con las personas.
Desperdicio por la fabricación de Defectos
Ya lo hemos platicado antes. El mundo es una enorme máquina de variabilidad. Una de las consecuencias de la variabilidad es la generación de defectos. Ahora, pensemos en un defecto. Esta es una pieza que compramos como materia prima, a la que le invertimos tiempo de nuestros trabajadores para trabajarla, tiempo de nuestras máquinas para transformarla, tal vez la juntamos con otros materiales y aumentamos su costo y… Termina siendo desperdiciada. O en el mejor (o será peor) de los casos, le invertimos tiempos extra, la retrabajamos y la vendemos como de segunda.
La variabilidad es una limitante de la productividad que no podemos evitar. Pero que sí podemos controlar. Para hacer esto, lo más indicado es hacer esfuerzos de control de la calidad y esfuerzos de reducción de la variabilidad por medio de proyectos de control estadístico de procesos y Six Sigma.
2. Mejorar el aprovechamiento de la Maquinaria o equipo
Ahora, tal vez tienes un proceso que produce pocos defectos, y tienes un diseño que maximiza el valor del cliente. Pero…¿Cómo se fabrica? ¿Aprovechas al máximo los activos físicos que tienes?
Si quieres mejorar el aprovechamiento de la maquinaria o el equipo que tienes disponible, te doy los siguientes consejos:
Reducir los tiempos en que la máquina funciona en vacío
Este consejo y el siguiente está fundamentado en la aplicación de conceptos de TPM.
TPM o Mantenimiento Productivo Total es un sistema de administración de capital de trabajo (Maquinaria e instalaciones). Nació en Japón en la planta de Denso por allá de los años 50 ‘s del siglo pasado. Se basa en reducir las 6 grandes pérdidas:
- Fallas en los equipos
- Pérdidas de tiempo por ajustes
- Paradas menores y tiempos muertos
- Velocidad reducida
- Defectos creados por el proceso
- Pérdidas por puesta en marcha
Imagina esto. Acaba de subir el costo de la gasolina. Conduces tu automóvil y tienes que cruzar las vías del tren. Sin embargo, tienes la mala suerte de que el tren cruza por sus vías justo antes de que puedas cruzar. ¿Qué haces? Lo más prudente sería poner el freno de mano y apagar el carro hasta que el tren termine de pasar. Así evitas consumir gasolina en vano. A esto se debe sumar el costo de oportunidad relacionado con tener esta máquina y no aprovecharla.
Lo mismo sucede con nuestros procesos. Si mantenemos operando la máquina sin producir, estamos desperdiciando energía y otros recursos. Cada minuto que la máquina pasa operando sin producir, nos está costando sin ver resultados.
Reducir los tiempos en que la máquina está detenida
Entonces podemos optar por detener la máquina. Sin embargo, resulta que las inversiones de capital son productivas cuando están produciendo. Aquí la solución ideal sería buscar un enfoque de TPM en el que eliminamos las pérdidas por paradas menores y tiempos muertos.
La herramienta diseñada para atacar este tipo de problemas es SMED. Con ella, podemos hacer cambios rápidos de modelo y continuar con el flujo de la producción lo más rápido posible.
Mantener estable el abasto de materiales
Ahora bien, para poder hacer trabajar continuamente, es imprescindible que las máquinas tengan material para ser alimentadas. Para lograr esto la implementación de Lean Manufacturing a lo largo de los procesos productivos nos ayuda a conectarlos y asegurar que se muevan al mismo ritmo.
Podemos lograr resultados similares utilizando buffers de trabajo en proceso o acumulando inventario antes de las máquinas. Pero esta es una solución que saldría muy cara. Lo mejor que podemos hacer es conectar los procesos para movernos al ritmo de la demanda. Podemos lograr esto con herramientas como Kanban y Celdas de Manufactura.
Facilitar la producción por estandarización de partes
Otra cosa muy sencilla que podemos hacer es reducir los motivos por los que las máquinas deban de cambiar su configuración. La estandarización es una solución muy elegante para combatir este problema. Muchas armadoras de autos usan este tipo de estrategias para facilitar su producción y reducir el número de variables que hay al momento de armar un producto. Parten de una base estándar y sobre ella construyen los diferentes modelos de automóvil.
3. Mejorar el aprovechamiento de nuestro tiempo disponible
En los puntos anteriores hemos hablado de los materiales y de las máquinas. Sin embargo, mejorar el aprovechamiento de nuestro tiempo disponible se centra en las personas. Piensa esto, todos tus colaboradores son partícipes del producto que están entregando. Entre todos se crea la calidad y se satisfacen las necesidades de los clientes. El trabajo total se reparte entre todo el equipo y se trata de hacer de la mejor manera. Pero… ¿Usamos el tiempo disponible de la manera adecuada?
Aquí hay cuatro cosas que podemos hacer para mejorar:
Reducir la duración del proceso
Para lograr esto, la mejor herramienta que podemos utilizar es Kaizen. La mejora continua es una herramienta que nos ayudará a mejorar de manera regular el desempeño de nuestros procesos. Reducir la operación nos hace más productivos, porque podemos sacar más productos de nuestro proceso en menos tiempo y con la utilización de los mismos recursos. Si aplicamos la filosofía de mejora todos los días, en el largo plazo se verán cambios impresionantes que tendrán un impacto directo en tus resultados.
Reducir las Horas-Hombre del proceso
Aunado al punto anterior, tal vez no es posible reducir la duración del proceso, pero sí podemos cambiar el trabajo manual dedicado al proceso. Hay muchas automatizaciones sencillas que por lo general son aplicables a todos los procesos que nos ayudan a reducir la cantidad de personas necesarias para realizar un producto.
Un consejo, si haces un proyecto Kaizen de este tipo y reduces la cantidad de personal necesario para un proceso, no despidas al personal excedente. Ubícalo en un área en la que pueda ser productivo o agregar más valor. Si los despides inmediatamente tendrás problemas la próxima vez que implementes un proyecto de mejora.
Establecer estándares de operación
En la sección anterior hablamos de la estandarización de las partes. También es vital estandarizar los estándares de operación de todos los procesos. De esta manera, podremos identificar situaciones normales de situaciones en las que produciríamos defectos. Si nuestro proceso es predecible, podemos hacer una mejor planeación para operarlo de la mejor manera y mejorar el aprovechamiento de nuestra mano de obra.
Redistribuir el trabajo
De manera similar a lo que hablamos en el punto sobre mantener el abasto de materiales, es importante que las personas tengan una distribución de trabajo equitativa. De esta manera podemos asegurar que el trabajo fluye armónicamente entre todos los procesos. Recuerda, aquí buscamos alinear los tiempos de operación de las personas para que independientemente del trabajo que se encuentren realizando, el tiempo de cada ciclo de producción sea similar entre todos ellos.
Para finalizar
Este artículo es un resumen de muchas de las herramientas que se han implementado en las plantas para mejorar la productividad. Sin embargo, es sólo la tercera de las 12 formas diferentes que existen para aumentar la productividad.